- Dans l'industrie automobile, il est employé pour souder des composants de batteries et des structures légères.
- Le secteur médical l'utilise pour la fabrication d'implants et d'instruments chirurgicaux.
Le soudage est un procédé utilisé dans de nombreux secteurs industriels pour assembler des matériaux métalliques et polymères avec précision. Parmi les différentes techniques existantes, le soudage au laser se distingue par sa rapidité, son apport thermique réduit et sa capacité à assembler des matériaux variés. Cette technologie repose sur l’utilisation d’un poste à souder laser, permettant une fusion localisée grâce à un faisceau concentré. Elle est employée dans des domaines comme l'automobile, l'aéronautique, le médical et l'électronique.
Quels sont les différents types de soudage ?
Soudage au laser
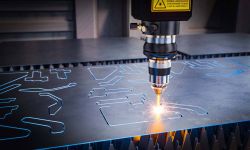
- Dans l'industrie alimentaire, il sert à assembler des contenants en acier inoxydable pour garantir l'étanchéité et l'hygiène des équipements de conditionnement.
- Dans l'aéronautique, ce procédé sans contact est appliqué à la fabrication de structures en alliages spécifiques, limitant les contraintes mécaniques et thermiques sur les pièces sensibles.
Soudage à l'arc
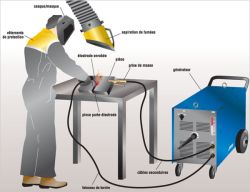
Ce procédé repose sur un arc électrique qui chauffe et fait fondre les matériaux. Il comprend plusieurs variantes :
- Soudage MIG/MAG (Metal Inert Gas / Metal Active Gas) : Un fil électrode continue sert de métal d'apport. Ce procédé est utilisé pour les structures métalliques et les carrosseries automobiles.
- Soudage TIG (Tungsten Inert Gas) : Une électrode en tungstène crée l'arc électrique. Ce procédé permet d'assembler des matériaux fins comme l'aluminium et l'inox.
- Soudage à l'électrode enrobée (MMA) : Une électrode fusible enrobée protège la soudure. Cette méthode convient aux travaux de maintenance et aux chantiers extérieurs.
- Soudage à l'arc plasma : Un jet de plasma ionisé concentre l'énergie de l'arc. Ce procédé est employé pour des soudures de haute précision dans l'aéronautique et l'industrie chimique.
Soudage par résistance
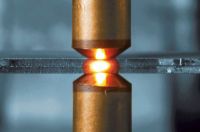
Ce procédé repose sur la combinaison de la pression et du courant électrique pour chauffer les pièces. Il comprend notamment :
- Le soudage par points, souvent utilisé en construction automobile.
- Le soudage par bossage, pour assembler des pièces épaisses.
Soudage par ultrasons
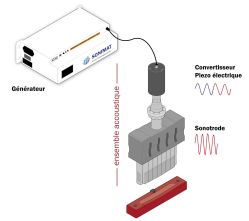
Le soudage par ultrasons utilise des vibrations mécaniques à haute fréquence pour générer une chaleur de frottement localisée, provoquant la fusion des matériaux au niveau de leur interface. Ce procédé est principalement utilisé pour l'assemblage de thermoplastiques et de certains métaux.
Il permet d'assembler rapidement des pièces sans nécessiter d'apport de matière ni d'adhésifs.
- dans l'industrie automobile pour la fixation de filtres et de composants intérieurs,
- dans le médical pour la fabrication de membranes et d'équipements stériles,
- dans l'électronique pour encapsuler des connecteurs et souder des composants sensibles.
Soudage par friction
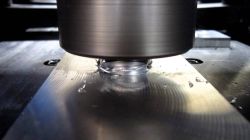
Le soudage par friction repose sur l'échauffement des matériaux par frottement, permettant leur assemblage sans fusion. Il existe plusieurs variantes selon le mouvement appliqué :
- Dans le soudage par friction rotative, une pièce tourne contre l'autre sous pression jusqu'à plastification locale.
- Le soudage par friction linéaire utilise un mouvement de va-et-vient rapide pour générer la chaleur nécessaire à l'assemblage.
- Le soudage par frottement malaxage fait intervenir un outil rotatif qui ramollit la matière et assure le mélange des matériaux.
Comment fonctionne un poste à souder au laser ?
Un poste à souder au laser est un équipement sophistiqué qui utilise un faisceau laser pour générer la chaleur nécessaire à la fusion des matériaux. Voici les étapes clés de son fonctionnement :
- Génération du faisceau laser : Le laser est produit par une source (fibre, CO2, YAG ou diode) et dirigé vers la zone à souder.
- Focalisation du faisceau : Le faisceau est concentré à l’aide de lentilles ou de miroirs pour atteindre une très petite zone, ce qui permet une précision extrême.
- Fusion des matériaux : Le faisceau laser chauffe rapidement les matériaux jusqu’à leur point de fusion, créant une zone de fusion localisée.
- Refroidissement et solidification : Une fois le faisceau retiré, les matériaux fusionnés se refroidissent et se solidifient, formant une soudure solide.
Ce processus peut être réalisé en mode conduction thermique (fusion en surface) ou en mode trou de serrure (fusion plus profonde avec évaporation du métal). Le poste à souder au laser est souvent équipé de systèmes de contrôle numérique pour ajuster la puissance, la vitesse et la focalisation du faisceau.
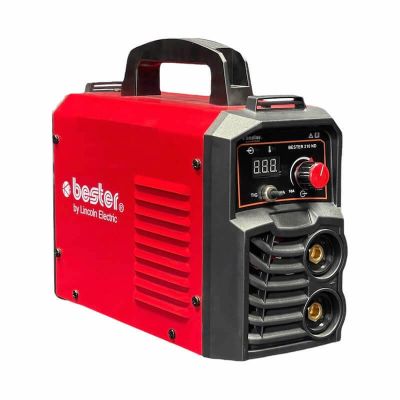
Quels matériaux peuvent être soudés au laser ?
Le soudage au laser est compatible avec une large gamme de matériaux, ce qui en fait une méthode très polyvalente. Voici les principaux matériaux soudables au laser :
- Métaux : Les aciers (doux, inoxydables, alliés), l’aluminium, le titane, le cuivre et le laiton sont couramment soudés au laser.
- Plastiques : Certains types de plastiques, comme le polypropylène et le polycarbonate, peuvent être soudés au laser, bien que cette application soit moins courante.
- Céramiques : Avec des lasers de haute puissance, il est possible de souder certaines céramiques, bien que cela nécessite des conditions spécifiques.
- Polymères : De nombreux thermoplastiques peuvent être soudés grâce au soudage laser par transparence.
Chaque matériau nécessite des réglages spécifiques en termes de puissance laser, vitesse de soudage et type de faisceau pour garantir une qualité optimale.
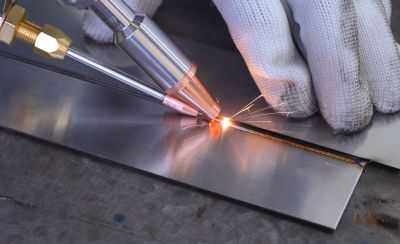
Quel gaz faut-il utiliser pour la soudure laser ?
Le procédé de fusion par faisceau lumineux nécessite l'utilisation de gaz de de soudage pour limiter l'oxydation, stabiliser le bain de fusion et influencer la pénétration du faisceau. Le choix du gaz dépend du matériau et des caractéristiques recherchées pour l'assemblage.
- Azote (N₂) : Cette protection gazeuse réduit la formation d'oxydes et modifie la structure métallurgique de certains aciers inoxydables.
- Argon (Ar) : Un gaz inerte qui protège la zone de soudure de l’oxydation et des impuretés.
- Hélium (He) : Il est utilisé pour les soudures nécessitant une pénétration profonde, notamment sur l'inox et le titane.
- Dioxyde de carbone (CO₂) : Ce gaz favorise l'ionisation du plasma et peut être utilisé pour ajuster la forme du bain de fusion sur certains métaux.
- Mélanges gazeux : Cette combinaison de plusieurs gaz ajuste la fluidité du métal en fusion et influence la formation des microstructures en fonction des besoins du soudage.
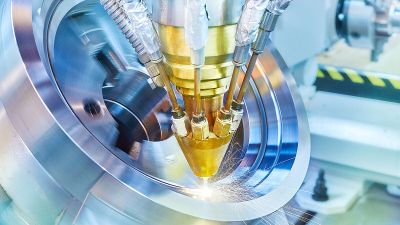
Quels sont les types de lasers utilisés en soudage ?
Soudure laser à fibre
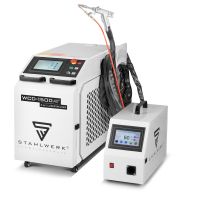
Soudure laser CO2
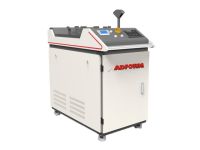
Soudure laser YAG
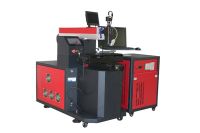
Soudure laser à diode
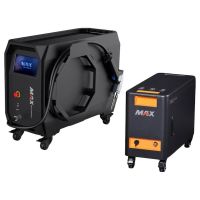
Quels sont les avantages du soudage au laser ?
Le soudage thermique localisé offre de nombreux avantages par rapport aux méthodes traditionnelles, ce qui explique son adoption croissante dans l’industrie. Voici les principaux atouts de cette technologie :
- Précision : Le faible apport thermique diminue les contraintes mécaniques et réduit les déformations des pièces assemblées.
- Vitesse : Le soudage laser permet des cadences de production élevées et de diminuer le temps de fabrication.
- Qualité de soudure : Les soudures réalisées au laser sont souvent plus propres et plus résistantes, avec moins de déformations.
- Maîtrise des coûts de production : Bien que le coût d'un poste à souder laser soit plus élevé que celui d'un équipement de soudage conventionnel, l'absence de consommables, la réduction des défauts et l'automatisation du procédé permettent d'amortir cet investissement sur le long terme.
- Polyvalence : Ce procédé peut être utilisé pour assembler des matériaux démontables, des feuilles métalliques fines ou des pièces épaisses.
- Automatisation : Le soudage laser peut être intégré aux chaînes de production robotisées, garantissant un résultat homogène et diminuant le taux de rebuts.
- Réduction des déchets : La précision du laser minimise les pertes de matériaux et les rejets.
- Réduction des opérations de finition : L'absence de métal d'apport et la finesse du cordon de soudure permettent de limiter les besoins en matériaux supplémentaires et en opérations post-traitement.