Sommaire
Cet article vous plaît ?
Partagez-le !
Temps de lecture estimé : 4min
Le détecteur de porosité permet de localiser avec précision les défauts d’isolation tels que les trous d’épingle, les microfissures ou les discontinuités dans les systèmes de protection anticorrosion. Utilisé aussi bien en atelier qu’en environnement opérationnel, cet équipement est soumis à des normes internationales strictes qui encadrent les méthodes d’essai, les paramètres techniques et les conditions d’application afin de garantir la fiabilité du contrôle. Ces normes permettent aux professionnels de s’assurer de la conformité des revêtements, de prolonger la durée de vie des installations, et de répondre aux exigences réglementaires et contractuelles propres à chaque secteur.
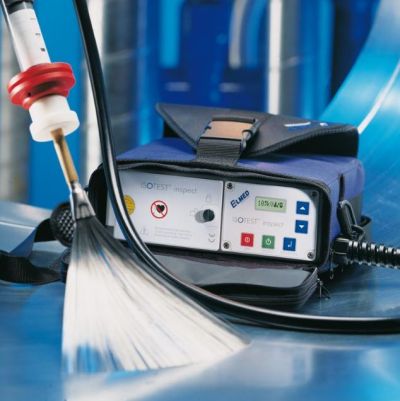
Devis pour un détecteur de porosité
Quelles sont les normes internationales encadrant les détecteurs de porosité ?
ISO 29601 : Référence pour les systèmes de peinture
La norme ISO 29601:2011 est une référence clé dans le domaine de la détection de porosité. Elle s’applique spécifiquement aux systèmes de peinture utilisés pour la protection anticorrosion. Cette norme définit les méthodes pour évaluer la porosité d’un feuil sec de peinture, quel que soit son épaisseur, sur un support métallique (acier ou autres métaux).
Elle décrit deux types de méthodes selon l’épaisseur du revêtement :
- Méthode basse tension (éponge humide) : adaptée aux couches fines.
- Méthode haute tension (étincelles) : utilisée pour les couches épaisses.
Cette norme vise les revêtements électriquement non conducteurs et peut être utilisée aussi bien pour les revêtements neufs que ceux en service. Elle est actuellement en cours de révision sous l’intitulé ISO/DIS 29601, signe de son actualisation continue en fonction des pratiques industrielles.
ISO 8289-A : Essai des couches anodiques
La norme ISO 8289-A traite des méthodes d’essai applicables aux couches anodiques sur aluminium, mais elle est également mentionnée dans le contexte plus large du contrôle de porosité des revêtements. Cette norme spécifie des techniques de détection de défauts dans les films anodiques, en particulier en présence de faibles conductivités, rendant son application pertinente pour les tests de porosité sur des substrats non métalliques ou spécialisés.
ISO 14654 : Essais non destructifs de porosité
La norme ISO 14654 s’inscrit dans le cadre des essais non destructifs. Elle précise les exigences relatives aux instruments de détection de porosité et aux procédures d’essai destinées aux revêtements appliqués sur des surfaces métalliques. Elle s’intéresse notamment aux critères de fiabilité et de reproductibilité des tests.
L’intérêt de cette norme réside dans sa rigueur technique, avec une définition précise des paramètres d’essai : tension, durée de contact, nature de la sonde, etc. Elle contribue à assurer une évaluation homogène et traçable de la porosité des revêtements dans un cadre industriel.
ISO 2746 : Détection de discontinuités dans les revêtements
La norme ISO 2746 complète les autres normes en encadrant les méthodes de détection de discontinuités, également appelées « vacances » ou « trous d’épingle », dans les systèmes de revêtement. Elle est particulièrement adaptée aux tests sur substrats métalliques, notamment dans les environnements exigeants tels que les installations marines ou pétrochimiques.
Elle précise les exigences en matière de calibrage des détecteurs de porosité, la préparation des surfaces, et les conditions environnementales optimales pour garantir un contrôle de porosité des revêtements fiable.
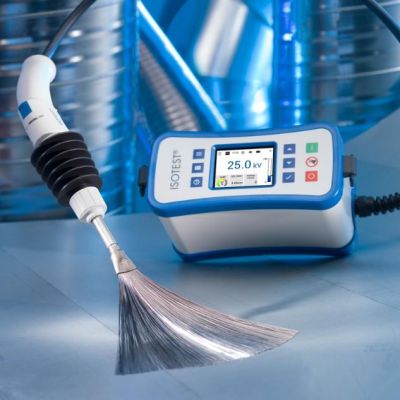
Quelles sont les critères techniques encadrés par les normes de détection de porosité ?
Épaisseur du feuil sec
L’épaisseur du revêtement constitue un paramètre fondamental dans les méthodes de détection de porosité. Les normes, notamment l’ISO 29601, imposent une sélection de l’équipement de test en fonction de cette épaisseur.
- Pour des revêtements fins (≤ 500 µm), la méthode dite de l’éponge humide à basse tension est privilégiée.
- Pour des revêtements plus épais (> 500 µm), les normes recommandent l’usage de détecteurs à haute tension par décharge électrique.
Ce critère permet de calibrer correctement la tension de test, afin de détecter efficacement les discontinuités sans endommager le revêtement.
Nature du support
Les normes distinguent les essais réalisés sur différents types de subjectiles. La plupart des tests s’appliquent à des substrats métalliques, notamment l’acier, en raison de leur conductivité.
- Les revêtements électriquement non conducteurs posés sur des supports métalliques sont les cas les plus courants encadrés par les normes.
- Le choix de la méthode dépend aussi de la sensibilité du support aux tensions appliquées, pour éviter les faux positifs ou les dégradations.
La connaissance du support est recommandée pour paramétrer un détecteur de porosité en conformité avec les exigences normatives.
Conditions d’application de la norme
Les procédures de contrôle de porosité des revêtements doivent être réalisées dans des conditions maîtrisées. Les normes encadrent plusieurs aspects :
- Température et humidité ambiantes, qui influencent la conductivité et le comportement du revêtement.
- Propreté de la surface : une surface contaminée (graisse, poussière, humidité) fausse les résultats.
- Accessibilité des zones testées : les détecteurs doivent pouvoir entrer en contact uniforme avec la surface.
- Absence d’interférences électriques ou magnétiques, qui pourraient altérer le signal de détection.
Ces conditions permettent d’assurer la validité du test et l’interprétation correcte des signaux détectés.
Conformité réglementaire et qualité des revêtements
Les normes techniques encadrent la qualité des revêtements par des critères d’acceptabilité. L’appareil de détection de porosité devient un outil d’audit de conformité dans les environnements réglementés.
- Une porosité détectée au-delà d’un seuil critique peut signifier un risque de corrosion prématurée.
- La conformité aux normes telles que l’ISO 29601 permet de démontrer la maîtrise des procédés de revêtement selon les exigences industrielles et contractuelles.
Les normes servent donc aussi à documenter la qualité des ouvrages revêtus, notamment pour les audits de certification ou les appels d’offres publics.
Maintenance et prolongement de la durée de vie des installations
La détection de porosité n’est pas réservée à la phase de production ; elle s’intègre aussi aux programmes de maintenance préventive.
- Les normes autorisent l’utilisation des méthodes d’essai sur des revêtements en service.
- Ces tests permettent d’évaluer l’évolution de la porosité au fil du temps, en lien avec l’exposition à des agents corrosifs.
Ainsi, le respect des critères normatifs permet d’anticiper les dégradations et de planifier les opérations de maintenance avant qu’une défaillance critique ne survienne.
Responsabilité professionnelle et traçabilité
L’usage normé du détecteur de porosité implique des obligations en matière de traçabilité technique.
- Les essais doivent être documentés, avec conservation des paramètres : tension appliquée, type de méthode, conditions ambiantes, résultats observés.
- Les résultats doivent être traçables et reproductibles, en vue d’un contrôle externe ou d’une expertise technique.
Les normes favorisent ainsi une responsabilisation des professionnels, tout en créant un socle d’assurance qualité dans le contrôle de porosité des revêtements.