Sommaire
Cet article vous plaît ?
Partagez-le !
Temps de lecture estimé : 4min
La détection de porosité joue un rôle de protection contre la corrosion, les agressions chimiques ou les pertes d’isolation électrique. Utilisés sur des structures métalliques, des pipelines, des équipements immergés ou des installations électriques, ces revêtements doivent être continus et exempts de défauts microscopiques. Le détecteur de porosité permet d’identifier efficacement les discontinuités, comme les fissures, trous d’épingle ou inclusions, qui compromettent l’intégrité du revêtement.
Devis pour un détecteur de porosité
Pourquoi faut-il contrôler la porosité des revêtements ?
Prévenir la corrosion prématurée des substrats
La principale raison de contrôler la porosité d’un revêtement réside dans la nécessité de prévenir la corrosion accélérée du substrat. Une porosité, même microscopique, constitue un point d’entrée pour l’humidité, les gaz ou les agents chimiques, favorisant ainsi les phénomènes d’oxydation. Dans le cas d’un revêtement appliqué sur un métal, la moindre discontinuité peut annuler l’effet barrière et provoquer une dégradation localisée qui s’étend rapidement si elle n’est pas détectée à temps.
Maintenir l’intégrité diélectrique du revêtement
Lorsqu’un revêtement a pour fonction de servir d’isolant électrique, toute porosité compromet directement ses performances. La détection de porosité devient alors une étape critique pour garantir que la résistance diélectrique est homogène sur toute la surface traitée. Une fuite de courant à travers une imperfection signale une discontinuité que seul un détecteur de porosité permet d’identifier efficacement.
Éviter les défauts liés au processus d’application
Les porosités sont souvent liées à des erreurs ou à des conditions défavorables lors de l’application du revêtement. Cela peut inclure :
- des coulures provoquant un film sec trop mince,
- des bulles d’air piégées relâchant des gaz à la surface,
- des cratères dus à l’humidité ou à une mauvaise fluidité,
- des sur-épaisseurs entraînant des fissures au durcissement,
- des sous-épaisseurs sur les angles ou les surfaces rugueuses.
Le contrôle par détection de porosité permet d’identifier ces défauts invisibles à l’œil nu et d’éviter les reprises coûteuses après durcissement.
Garantir la performance à long terme des revêtements
Dans les milieux industriels exposés à des contraintes mécaniques, chimiques ou thermiques intenses, l’assurance qualité des revêtements est une exigence incontournable. Une porosité non détectée peut engendrer des défaillances fonctionnelles majeures sur des équipements critiques. Le contrôle par détecteur de porosité contribue ainsi à fiabiliser les systèmes de protection dans la durée et à limiter les coûts de maintenance non planifiés.
Répondre aux exigences normatives
Le contrôle de la porosité est également imposé par les normes techniques telles que la NF EN ISO 29601, qui spécifie les méthodes de vérification de l’absence de discontinuités dans les revêtements anticorrosion. Utiliser des méthodes validées de détection de porosité, comme l’éponge humide ou le balai haute tension, permet d’assurer la conformité réglementaire des procédés de protection de surface.
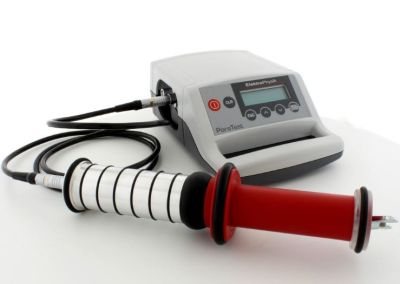
Quand faut-il effectuer un test de porosité sur des revêtements ?
Avant la mise en service d’un revêtement
Un test de porosité doit impérativement être réalisé avant la mise en service d’un revêtement, notamment lorsqu’il est appliqué sur un substrat métallique. Cela permet de vérifier l’absence de défauts critiques, tels que des piqûres, trous d’épingle ou fissures, qui compromettraient la continuité du revêtement et entraîneraient une corrosion prématurée du support. Ce contrôle est essentiel pour garantir que le revêtement remplit pleinement sa fonction protectrice et diélectrique, en particulier dans les secteurs industriels sensibles.
Après une opération de retouche ou de réparation
Toute opération de retouche ou de reprise partielle d’un revêtement doit être suivie d’un test de porosité localisé. Cela permet de s’assurer que les zones réparées sont exemptes de discontinuités et présentent une homogénéité satisfaisante avec le reste du revêtement. L’utilisation d’un détecteur de porosité garantit alors la fiabilité du contrôle dans les zones critiques.
Lorsqu’un revêtement est destiné à des environnements sévères
Il est nécessaire d’effectuer un test de porosité lorsque les revêtements sont exposés à des conditions extrêmes, telles que l’immersion, les zones de marnage ou les atmosphères classées à haute corrosivité (catégorie C5). Dans ces contextes, même une faible porosité peut induire des phénomènes de dégradation accélérée, ce qui justifie un contrôle exhaustif via des méthodes de détection de porosité adaptées.
En fonction de l’épaisseur du revêtement
La fréquence et la méthode de contrôle varient également selon l’épaisseur du revêtement :
- Pour une épaisseur sèche inférieure à 500 µm, un test à l’aide d’un détecteur de porosité à éponge humide est recommandé.
- Pour une épaisseur comprise entre 500 µm et 8 mm, le test se réalise avec un détecteur de porosité haute tension. Ce contrôle est particulièrement important pour les revêtements épais, souvent appliqués sur des structures à forte sollicitation.
Quelles sont les principales méthodes de contrôle de porosité des revêtements ?
Détection de porosité par méthode à éponge humide (basse tension)
Cette méthode repose sur l’utilisation d’un détecteur de porosité à éponge humidifiée, reliée à une source de basse tension (environ 90 V). Elle est adaptée aux revêtements dont l’épaisseur sèche est inférieure à 500 µm. Le principe consiste à appliquer une tension entre l’éponge et le substrat métallique. Si l’éponge traverse une zone de porosité, le liquide entre en contact avec le métal, fermant ainsi le circuit électrique et déclenchant une alarme visuelle ou sonore. Ce procédé permet une détection rapide et non destructive des discontinuités sur des surfaces traitées.
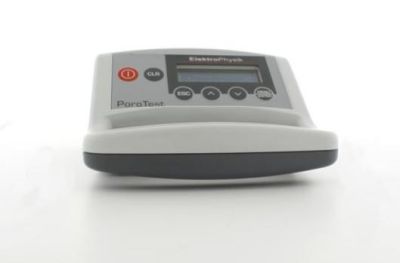
Détection de porosité par balai électrique haute tension
Pour les revêtements d’épaisseur plus importante, entre 500 µm et 8 mm, la méthode à haute tension est privilégiée. Elle utilise un balai électrique relié à une tension réglable, généralement comprise entre 1 et 30 kV. Lors du passage du balai sur le revêtement, une discontinuité provoque la formation d’un arc électrique, signalant immédiatement le défaut par une alarme. Ce type de détecteur de porosité permet la couverture de grandes surfaces et s’avère particulièrement utile pour les structures industrielles ou les pipelines.
Observations micrographiques
L’inspection micrographique consiste à examiner la surface du revêtement à l’aide d’un microscope métallographique. Elle permet d’identifier des porosités ou des fissures de taille supérieure au pouvoir séparateur de l’instrument optique. Cette méthode, recommandée par la norme NF EN ISO 12540 pour certains types de dépôts comme le chrome, fournit une analyse précise, mais reste principalement applicable dans des contextes de laboratoire ou d’analyse de contrôle qualité poussée.
Techniques électrochimiques de détection de porosité
Certaines méthodes plus avancées reposent sur la mesure de la résistance de polarisation ou de la constante diélectrique du revêtement. Ces approches sont adaptées à la détection de porosités de très petite taille, non visibles à l’œil nu. Elles consistent à envoyer des signaux électriques à haute fréquence à travers le matériau, puis à analyser les variations de réponse pour identifier la présence de porosité interne. Bien que très précises, ces méthodes relèvent souvent du domaine de la recherche ou de l’expertise spécialisée.
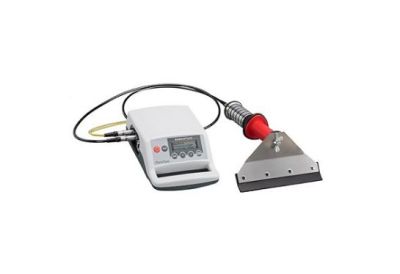
Contrôle de porosité par peigne ou balai diélectrique
Employée notamment pour les matériaux composites ou les isolants électriques, cette technique utilise des équipements spécifiques (balais ou peignes diélectriques) pour mesurer les variations de la constante diélectrique du revêtement. Les capteurs intégrés aux dispositifs détectent les anomalies par perturbation du signal électrique. Cette méthode non destructive est très utilisée dans le contrôle qualité de matériaux techniques, y compris les revêtements polymères ou diélectriques.